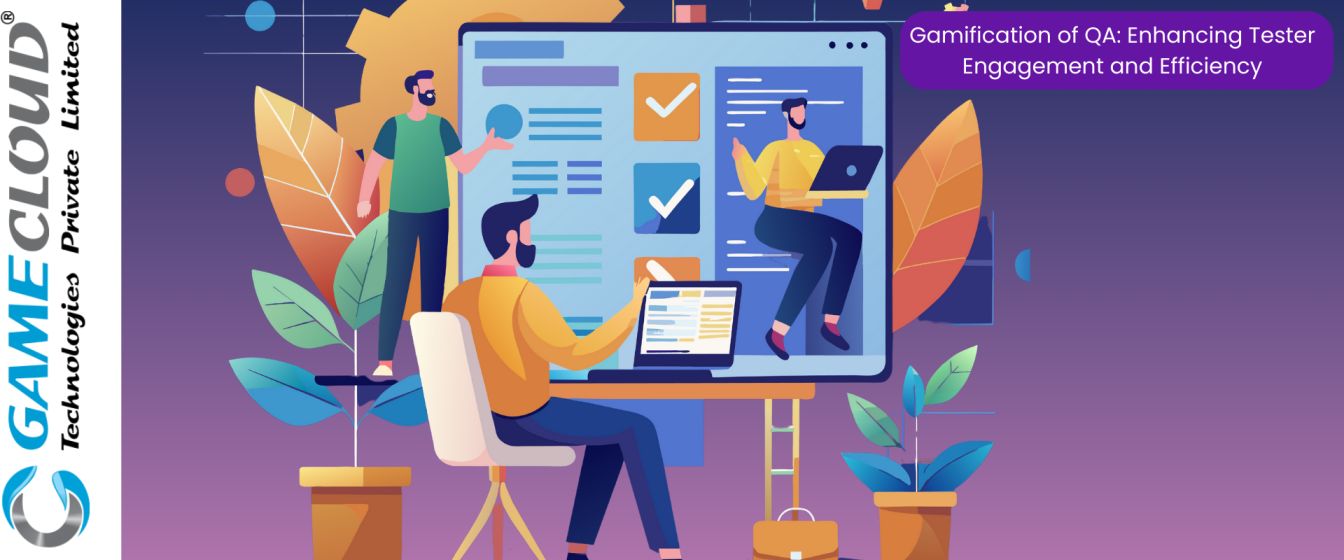
Gamification is the application of game-like elements, such as points, badges, and leaderboards, in non-game environments to boost motivation and engagement. While initially popular in entertainment and education, gamification has now found a growing foothold in corporate sectors, including product manufacturing. By infusing game mechanics into manufacturing workflows, companies can significantly improve employee engagement and productivity.
In manufacturing, gamification transforms routine and often repetitive tasks into motivating challenges. Research suggests that gamified environments can increase productivity by 20% and improve engagement levels by as much as 47%. When applied effectively, gamification not only keeps the workforce motivated but also enhances the quality of production, ultimately leading to faster turnaround times and higher satisfaction for both employees and managers.
The Role of Gamification in Manufacturing: A Strategic Approach
Gamification in manufacturing introduces game mechanics—such as points, badges, and rewards—into daily operations. These elements turn routine production activities into stimulating tasks that encourage employees to remain motivated and focused on achieving specific goals. Traditional manufacturing tasks can sometimes lead to disengagement due to their repetitive nature. This decline in motivation can reduce overall productivity and affect the quality of the final product.
By integrating gamification into the manufacturing process, companies can transform mundane activities into enjoyable and competitive challenges. For example, workers can earn points for meeting production quotas, maintaining high accuracy, or achieving safety milestones. Team-based activities can also be gamified, where teams compete to achieve the best efficiency ratings or lowest defect rates, contributing to a more engaging and collaborative workplace environment. This dynamic helps employees feel a sense of accomplishment, improving both individual and team performances.
Boosting Employee Engagement and Productivity through Gamification
Introducing gamification into the manufacturing process can lead to a significant boost in employee morale and motivation. Elements like points, badges, and leaderboards provide a sense of achievement and healthy competition, encouraging employees to stay engaged in their tasks. This not only reduces monotony but also helps employees maintain focus, thus minimizing errors and inefficiencies.
For example, consider a random product like smartphone assembly. Gamification could be applied by rewarding workers who achieve consistent high-quality assembly or meet specific productivity targets, such as assembling a certain number of devices without defects. Teams could also compete on metrics such as assembly speed, defect reduction, or adherence to safety protocols, earning points for each milestone achieved. By actively participating in this system, employees would be more likely to engage with their tasks, take pride in their work, and continually strive to improve.
Additionally, gamification can help alleviate burnout, which is common in high-volume production environments. By introducing elements of fun and challenge, gamification turns repetitive tasks into opportunities for achievement. Friendly competition among workers, coupled with team challenges, creates an environment where individuals and teams strive to improve their performance, leading to higher output and fewer errors.
Research indicates that gamified manufacturing environments can lead to a 20% improvement in productivity, with employee engagement increasing by nearly 50%. Moreover, this competitive yet collaborative atmosphere allows teams to problem-solve more creatively, leading to better solutions and improved product quality.
Challenges and Best Practices in Implementing Gamification for Manufacturing
While the benefits of gamification in manufacturing are clear, there are challenges that companies must navigate when introducing such systems. One potential issue is the risk of fostering an overly competitive atmosphere, which could lead to unhealthy rivalry or increased stress among workers. Poorly designed gamification systems can also disengage employees if the mechanics seem forced or disconnected from actual production goals. For example, focusing solely on speed may encourage workers to rush through tasks, compromising product quality.
To avoid these pitfalls, companies should design gamification elements that align closely with both individual and team performance objectives. Clear metrics and fair reward systems should be established to promote a culture of continuous improvement rather than competition for the sake of winning. Balanced approaches, such as team-based challenges and collaborative rewards, can foster unity and reduce rivalry while still maintaining the competitive spirit.
It is also critical to ensure that gamification supports the broader goals of quality, safety, and efficiency. For example, badges or rewards could be earned not just for speed but also for maintaining safety protocols or reducing waste, ensuring that the focus remains on overall production excellence.
GameCloud: Elevating Product Quality Through Gamified Processes
At GameCloud, we believe in applying innovative solutions, such as gamification, to enhance production and quality. With a traditionally focused approach towards video game QA Testing and interactive entertainment softwares, we recognize the potential of gamified systems in various sectors, including manufacturing. By incorporating game-like mechanics into production processes, we help clients optimize workflows, boost workforce engagement, and ensure higher-quality output.
Conclusion
Gamification in the product manufacturing process offers significant benefits by increasing employee engagement, enhancing efficiency, and improving overall product quality. By integrating game-like elements into daily operations, manufacturers can create a more dynamic and enjoyable workplace where employees remain motivated, collaborate more effectively, and consistently deliver high-quality products. In the long term, this approach can lead to higher productivity, reduced error rates, and greater innovation, ultimately contributing to a more successful manufacturing operation.
For Know More Contact-Now
FAQs for: Gamification of QA: Enhancing Tester Engagement and Efficiency
What is gamification, and how is it applied in QA processes?
Gamification involves integrating game-like elements, such as points, badges, and leaderboards, into non-game environments. In QA processes, it is used to enhance engagement and efficiency by turning routine testing activities into motivating challenges. This approach helps QA testers stay focused, improve productivity, and maintain high standards of quality in their tasks.
How does gamification improve employee engagement in manufacturing QA?
Gamification fosters a sense of accomplishment and healthy competition through rewards for achieving milestones such as meeting quality targets or reducing errors. These game-like elements make repetitive tasks more enjoyable and engaging, boosting morale and motivation while minimizing burnout in high-volume production environments.
What are the potential challenges of implementing gamification in QA?
Challenges include the risk of creating an overly competitive environment that may increase stress or unhealthy rivalry among employees. Poorly designed gamification systems might also focus solely on metrics like speed, compromising quality. To address these issues, gamification strategies must align with broader goals, such as maintaining safety and ensuring high-quality outcomes.
What best practices should companies follow when implementing gamification in QA?
Companies should design gamification systems that align with individual and team performance objectives, incorporating balanced metrics that reward both speed and quality. Collaborative challenges and clear reward systems can foster unity while maintaining motivation. Ensuring that gamification supports overall goals like safety, efficiency, and waste reduction is essential for its success.
How does GameCloud support gamification in QA processes?
GameCloud integrates gamified systems into QA workflows to optimize efficiency and boost tester engagement. By leveraging game-like mechanics such as points and leaderboards, GameCloud helps clients create dynamic testing environments that enhance productivity, reduce errors, and ensure high-quality outcomes across various industries, including manufacturing.